In the poultry industry, margins are razor-thin, and every penny spent needs to pull its weight. For too long, poultry companies have leaned on diagnostics and contract labs as a crutch, ticking compliance boxes and relying on gut instinct to make important decisions. But outdated tools and guesswork does not make for a reliable strategy, and more tests aren’t the answer.
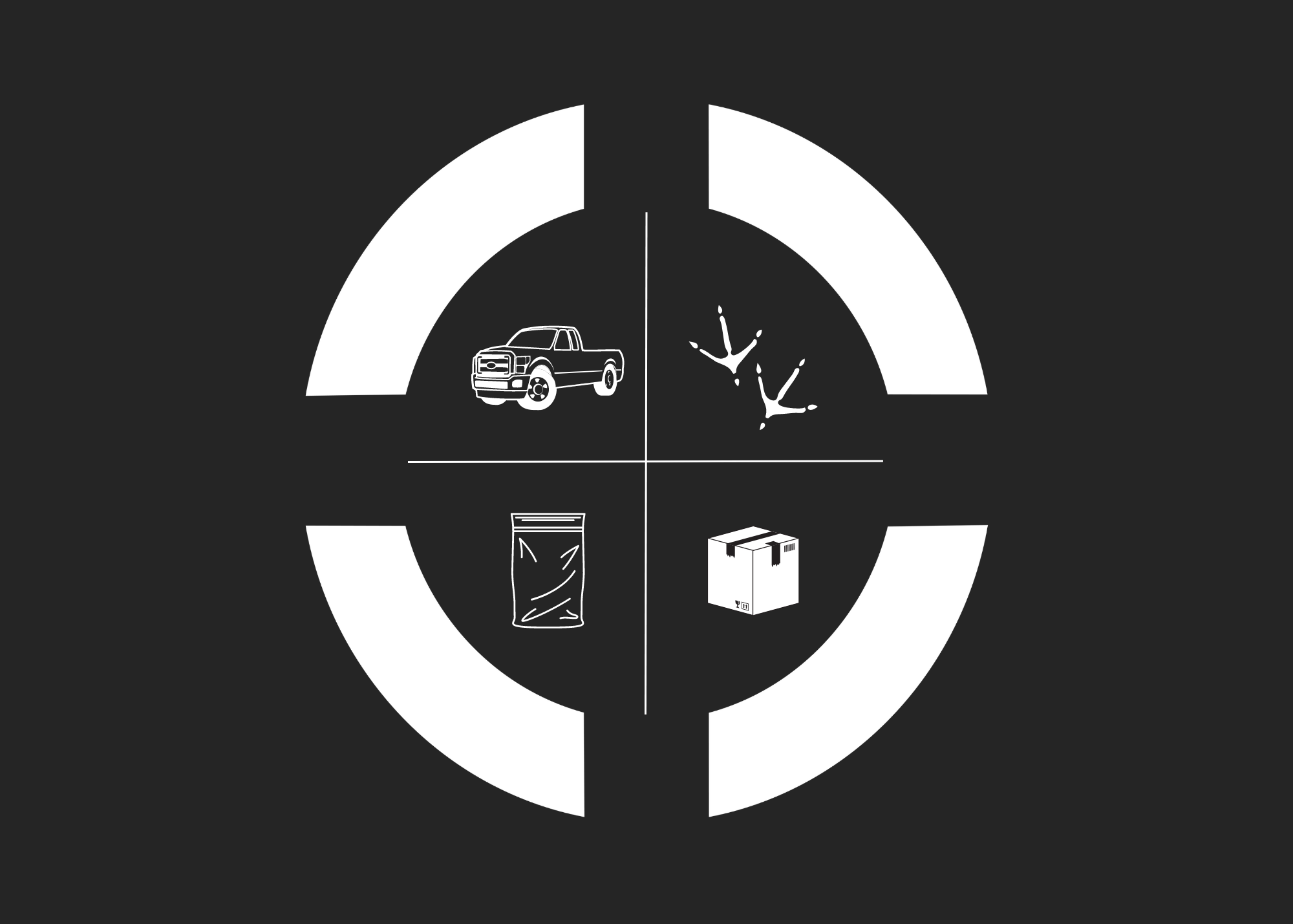
Publication
From the Field to the Lab: Behind the Scenes with Ancera (Part 1)
By Michael Lapides, Head of Marketing @ Ancera
How does Ancera turn chicken feces into valuable analytics?
In this series, I shadow and interview the team members responsible for each step in turning samples into actionable information.
Today I go to Northeast Georgia where Nick Hodgson leads Ancera’s Live Poultry Strategy.
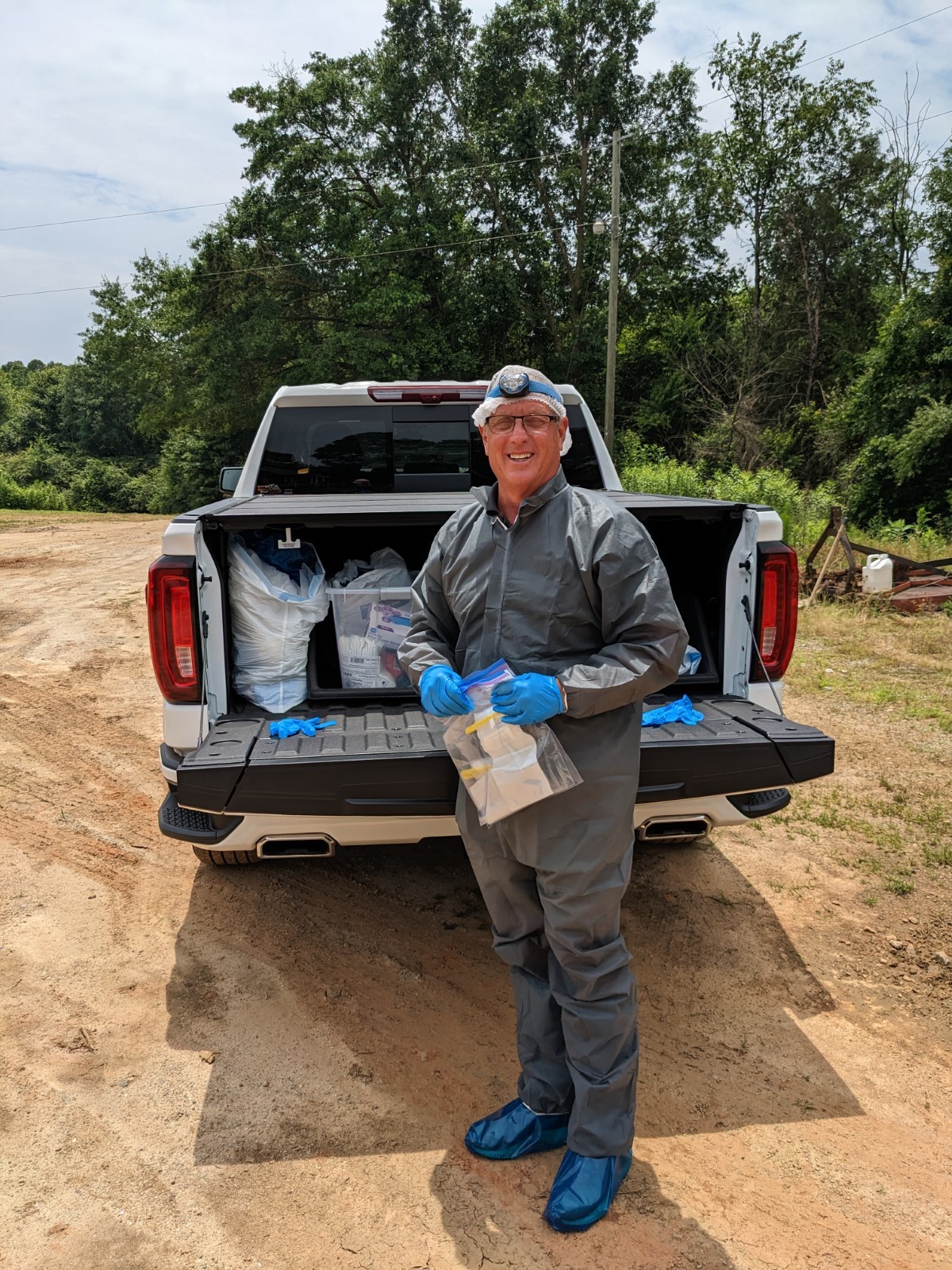
Trading in my office khakis for poultry coveralls, I left my daily marketing routine to experience the frontlines of Ancera’s operations — the poultry houses where Ancera collects data and ultimately improves production outcomes.
To recap, Ancera’s mission is to improve food productivity and safety. In the poultry industry we do this by providing real-time visibility that our customers have never had access to, allowing them to reduce threats and increase margins.
In the case of our flagship Coccidia System Monitoring (CSM) product, Ancera provides Oocyst per Gram (OPG) counts to characterize the pattern of Coccidia cycling over the course of a grow-out. When combined with control program information, production data, and Ancera's proprietary data models, the CSM product provides quantifiable metrics and actionable insights toward preventing unnecessary economic losses.
This powerful analytics engine runs on data collected directly from the poultry farms.
To learn more about this critical process in Ancera’s operations, I join our Director of Live Poultry Strategy, Nick Hodgson, as he takes me across Northeast Georgia to three broiler farms and answers my questions about how Ancera generates data for our customers.
Here’s an excerpt from our conversation:
ML: Tell me about your background. How did you get into poultry and eventually find yourself at Ancera?
NH: After graduating from San Diego State University I started working in the poultry industry. I’ve worked for integrators and primary breeders across a variety of live ops roles. One day I got a call from Arjun [Ancera’s CEO] who pitched me on the idea of using new technology to monitor for OPGs to better manage Cocci. I asked my friends what they thought and the rest is history.
ML: What does a day in the life of an Ancera Field Ops employee look like? What’s our itinerary for today?
NH: We’re going to drive to three grower farms to collect samples and ship them to a lab for immediate testing and trend analysis. The customer and our data science team collaborated on a sampling plan that tracks nearly half of their 300+ farms throughout the year. Ancera will do collections three to five times a week, based on customer use cases, and track grow-outs over a wide range of contract farms throughout their complex.
ML: Planning these sample collections must require some prep work. How do you go about this?
NH: It does indeed. It’s a carefully planned process Our engineering team gets placement data from the customers’ systems. I then put together the schedule two weeks in advance based on customer asks. The customer has communicated the ages and use cases they want to sample for, so today we’ll collect at farms where the birds are the respective ages. When we collect multiple data points over time for the farm, we create OPG curves, or time series, that analyzes the production trends for each flock.
ML: Can you give me an idea of what the customer ultimately sees in the product?
NH: Absolutely. Our aim is to provide a real-time view of the customer's operations. We'll collect data from a variety of farms that perform at high, medium, and low levels based on their six-flock average. This helps the customers understand the impact of Coccidia on their performance, either as a whole or down to individual farms. Getting visibility before a posting session means that customers get visibility and make improvements during a grow-out. We’ll also integrate the OPG data with settlement history so they can quantify how Cocci impacts performance.
ML: What’s the rationale behind collecting a specific number of samples?
NH: That's driven by our statistical models. As you can imagine, you cannot sample all 25,000 birds in a given house. We’ll typically sample multiple houses per farm and collect multiple samples in each house to power our epidemiological models. This is really important because you don't want to pool and lose information about the different cycling that is happening across the birds in the house. The approach offers a non-lethal, non-invasive alternative by collecting fecal samples for lab analysis. The samples are going to go through Ancera’s PIPER instrument and data science models to spot trends across the complex and farm levels.
ML: Your truck is loaded with PPE and shipping materials. Can you tell me more about the equipment that we need for today?
NH: We prep Whirl-Pak bags the night before to collect the samples. Each contains a bar code number that correspond to the farm, house, and sample ID. The samples are stored in a refrigerator which keeps the samples cool going into the lab. I fill out a Chain of Custody form and include that before sending the samples via FedEx out for overnight shipping for immediate processing.
ML: Biosecurity must be a significant concern. How do you ensure that we’re following the right protocols.
NH: Biosecurity is critical. Upon arrival, we disinfect our tires and sign in on the guest sheet. We also don full PPE before entering any house. As courtesy and to ensure we're invited back, we make it a point to explain our purpose to the on-site grower or technician.
ML: How do you plan to scale up this process as Ancera signs more customers?
NH: Scaling up is definitely on our radar. Our first customers have the opportunity to opt into our whiteglove service, but customers sometimes do their own sampling if they prefer. As for internal strategies, we have a trained team in place who understand biosecurity. As we scale, we're spending time hiring the right people and leveraging technology to automate or fool-proof every stage in the collection to analysis process.
ML: Thank you for letting me tag along. I’m excited to see the process firsthand.
NH: You bet.
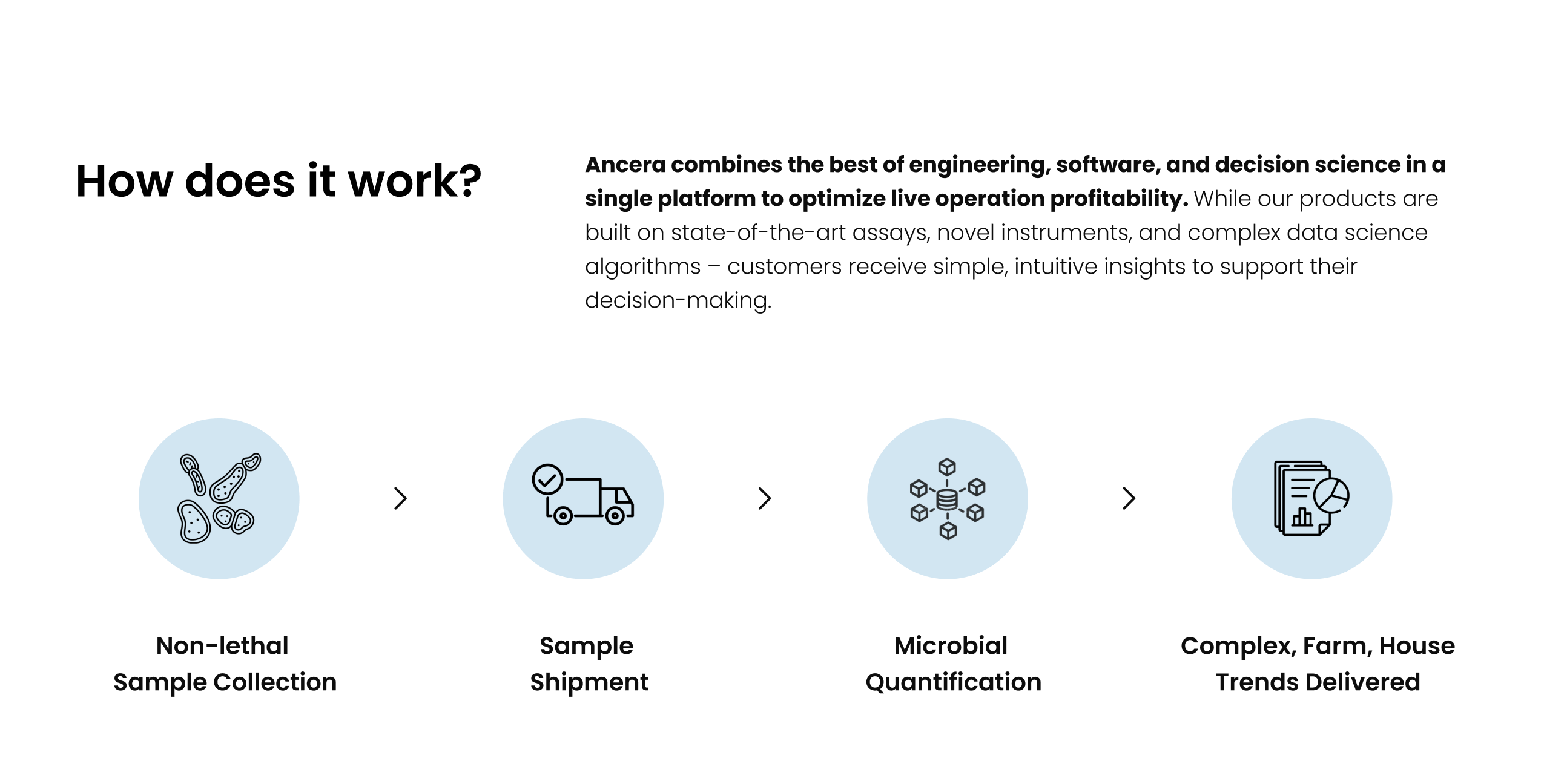
What impressed me the most about Nick’s process was his discipline when it came to the details. Inside the poultry houses I would catch Nick being picky over each sample, rigorously making sure they met our specifications so the lab team can reliably assay and quantify the Oocysts on the PIPER instrument.
Analytics products are only as good as their underlying data.
Next time we’ll follow the samples’ journey to the lab and provide a behind the scenes peak at what happens next.