In the poultry industry, margins are razor-thin, and every penny spent needs to pull its weight. For too long, poultry companies have leaned on diagnostics and contract labs as a crutch, ticking compliance boxes and relying on gut instinct to make important decisions. But outdated tools and guesswork does not make for a reliable strategy, and more tests aren’t the answer.
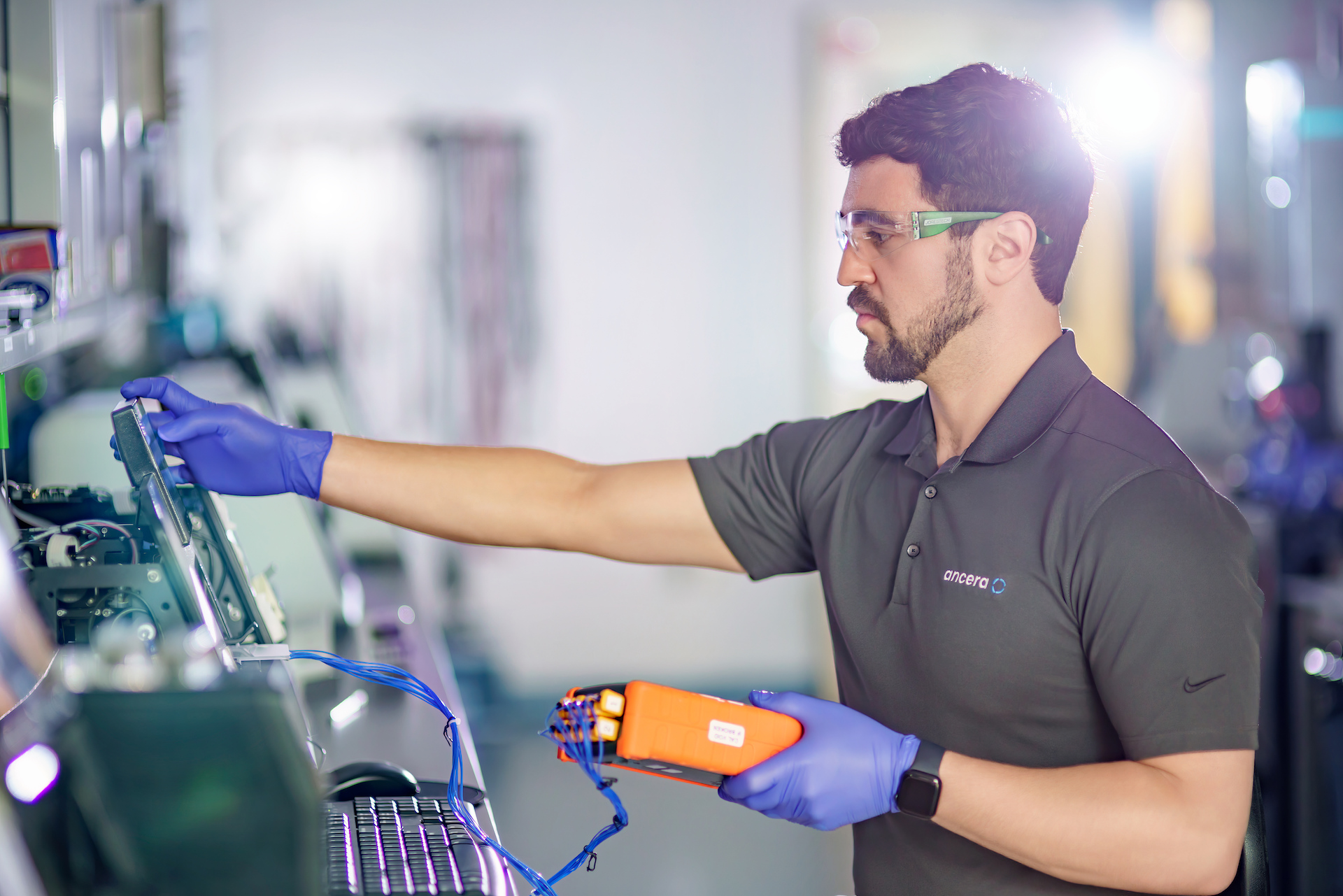
Publication
Under the Microscope: Behind the Scenes with Ancera (Part 2)
By Michael Lapides, Head of Marketing @ Ancera
How does Ancera turn chicken feces into valuable analytics?
In this series, I shadow and interview the team members responsible for each step in turning samples into actionable information.
Today I go to Ancera’s Laboratories in Branford, Connecticut where Matt Zwilling leads the company’s on-premise Engineering and Operations, as well as outsourced partnerships.
In Part 1 of our Behind the Scenes series, Nick Hodgson demonstrated the importance of scheduling, biosecurity, and sample integrity in our field operations. These samples were sent to Ancera’s lab as a part of our monitoring platform in order to analyze and ultimately generate high-value analytics that improve our customers’ operations. I again go through a mandatory wardrobe change and don the pre-requisite PPE required to experience Ancera’s R&D and production lab facilities.
Today, food producers are heavily investing their operational expenditure on feed, control programs, diagnostics, and information systems. Despite these critical inputs, companies are losing between $1M to $13M each week converting feed into protein. Ancera’s mission to improve food productivity and safety has never been more critical.
Our core thesis is that businesses require new visibility and software capabilities to generate the intelligence required to unlock new profits in a margin-intensive industry. In the case of Ancera’s Coccidia System Monitoring (CSM) product, we provide new visibility at scale through proprietary diagnostic instruments and assays using lab automation technology. More specifically, counting Oocysts per Gram (OPGs) to characterize the pattern of Coccidia cycling over the course of a grow-out and analyzing in conjunction with production data to produce insights that prevent economic losses.
Ancera’s labs are where these next-generation instruments pioneer the future of food production innovation and produce new visibility for our customers.
To learn more about these facilities, Ancera’s Director of Engineering and Operations, Matt Zwilling, escorts me through the various labs, telling me what I’m allowed to photograph and answers my questions.
Below is an excerpt from our conversation:
ML: Matt, first of all thank you for the tour. I remember from our Health and Safety Policies that we’re going to encounter some biohazardous materials today. What guidelines should I follow?
MZ: We’re going to wear full PPE — that includes lab coats, gloves, safety glasses, and closed toed shoes. Any samples or instruments will be worked on solely by lab employees, all of whom undergo annual safety and proficiency testing.
ML: Can you briefly describe the types of laboratories at Ancera’s headquarters and the function of each one in our operations?
MZ: Certainly. Let’s break them down into two categories. On the R&D side, there are five spaces — Microbiology, Macrobiology, Engineering, Chemistry, and Prototyping. Each are designed for specific purposes but work together to move our technology forward, whether it’s a novel microbial label or a new diagnostic instrument.
Second are the production labs (Figure 1), which functions like a company within a company to preserve the integrity of our customers’ samples. They have their own infrastructure, dedicated shipping and receiving, data entry rooms, and sample storage facilities. Only specific trained workers operate in the production labs, spanning across various functions such as microbiology, molecular biology, sequencing, and novel PIPER-based diagnostics.
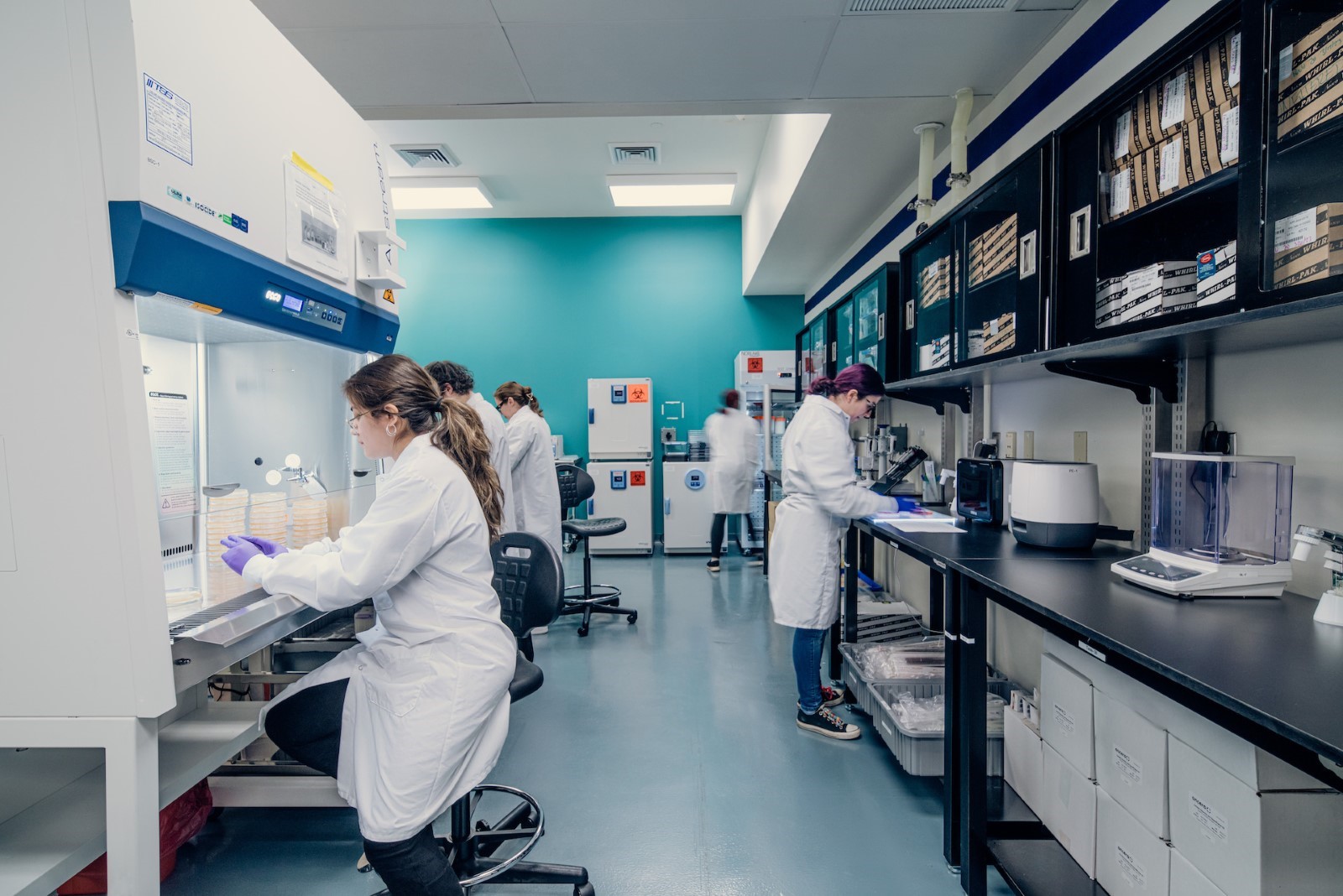
ML: And the PIPER testing is where the Coccidia samples are observed, correct?
MZ: That’s right. Field samples come through a dedicated receiving room separate from non-laboratory operations. They’re organized and logged into our Laboratory Information Management System (LIMS) and then stored in a dedicated refrigerator until processing. All samples go through Quality Control as they come into the lab to ensure the integrity of each sample, such as deviations in temperature or condition. We also process each sample in the Whirl Pak bag to ensure its traceability, scanning the bar code to check it into the PIPER for testing (Figure 2).
PIPER does two things extraordinarily well — it separates signal from noise in a world-class way, using MagDrive technology, fluorescence microscopy, and computer vision to reliably count and classify microorganisms of interest versus background litter and other organic materials. It also is unique in its ability to scale. PIPER doesn’t require human intervention, automating what would otherwise be tedious processes prone to human error.
We have several devices and each device can run multiple independent tests simultaneously, offering a new standard for high-cadence high-throughput diagnostics.
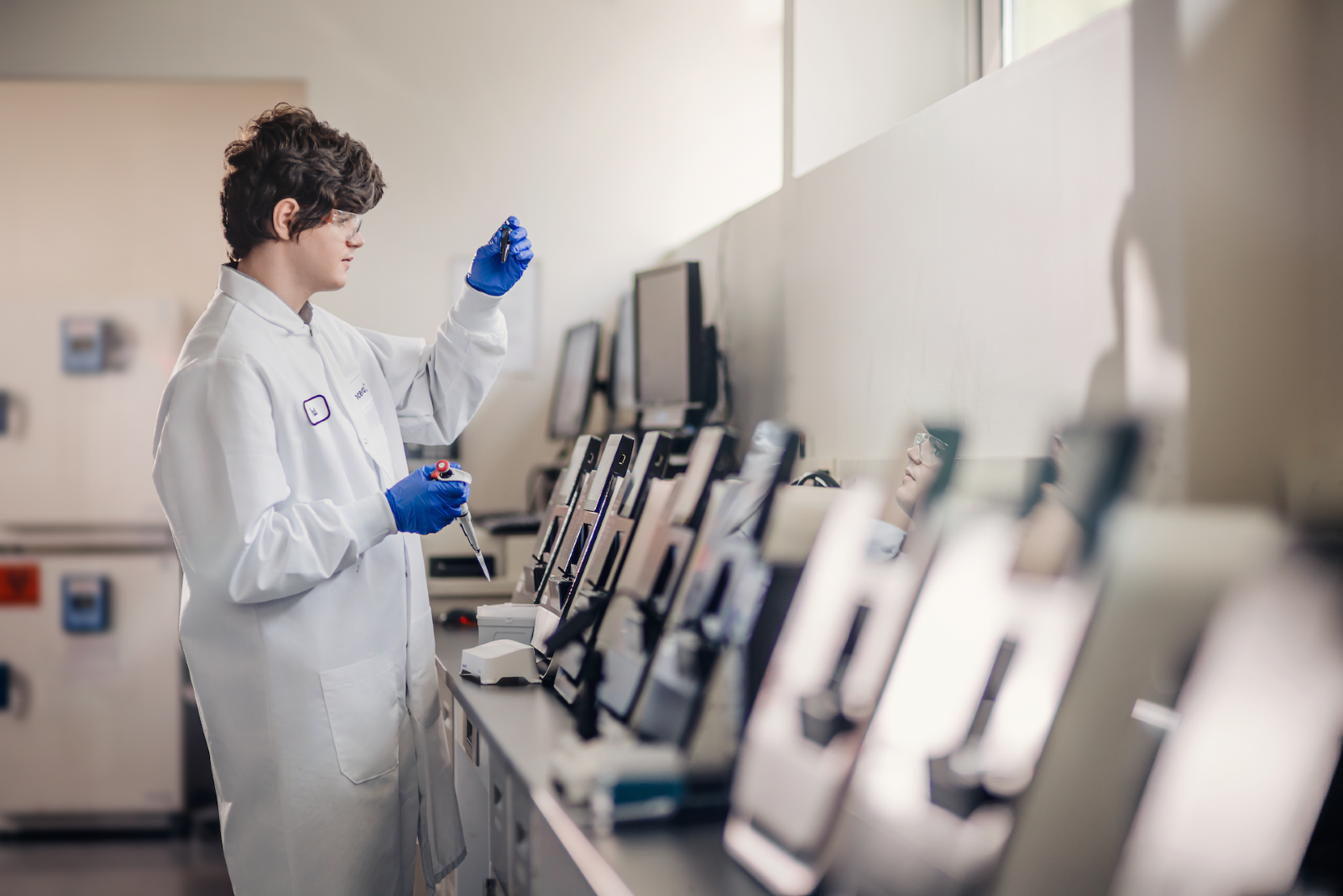
ML: How does this compare to other facilities and diagnostics in the Animal Ag and Food Safety industries?
MZ: Since we are talking specifically about PIPER today, the next closest diagnostic would be a Hemocytometer test. Conservatively speaking, a single Ancera lab worker can run more than 10x the number of samples using PIPER (Figure 3). For example, with Coccidia, we are utilizing automated fluorescence microscopy and deep learning algorithms to quantify and categorize Oocysts, whereas legacy techniques rely on the human eye. We also partner with select facilities to form a network of cloud labs, strategically located near customer sites.
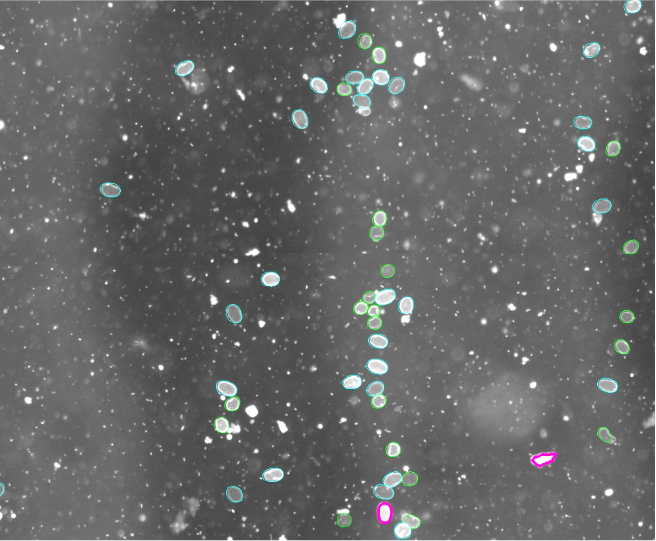
ML: What advice would you give a candidate looking into a job opportunity at Ancera’s laboratories?
MZ: We’re looking for a unique combination of values in our labs. On the R&D side we want you to think without any constraints. We’re building tools and capabilities never before seen in the industry so we’re looking for people that are open-minded in their approach to problem solving. A successful R&D worker can think about a customer’s problem and apply first principles to find the best possible solution — even if it's not with PIPER. The upside is that compared to most R&D roles, your work is destined for production, solving real problems for our customers.
On the production side, we emphasize discipline and professionalism in addition to intellectual curiosity. It’s about quality above all else. While the production lab team works in a separate area, they still need to be comfortable working on the cutting edge of technology and collaborating with R&D teams through software and whiteboards.
ML: Thank you for the behind-the-scenes glimpse into our IP and facilities. Our customers are shielded from the complexity of assays and diagnostics and simply get the insights generated in this lab. Is there anything else you’d like to share that you think Ancera’s customers would find useful?
MZ: Absolutely. Our operating standard is designed to build customer confidence in our data. I’ve drawn on prior experience in the aerospace and surgical device manufacturing industries to inspire our lab standards. In aerospace, we operated under ITAR standards for every product. Likewise, Ancera’s contract manufacturers apply FDA-level standards when building our products. In the lab, this mindset assumes that every sample is biohazardous and can cross-contaminate, adversely impacting results. The additional processes are rigorous, but this is how you get the highest quality data and information going back to customers.
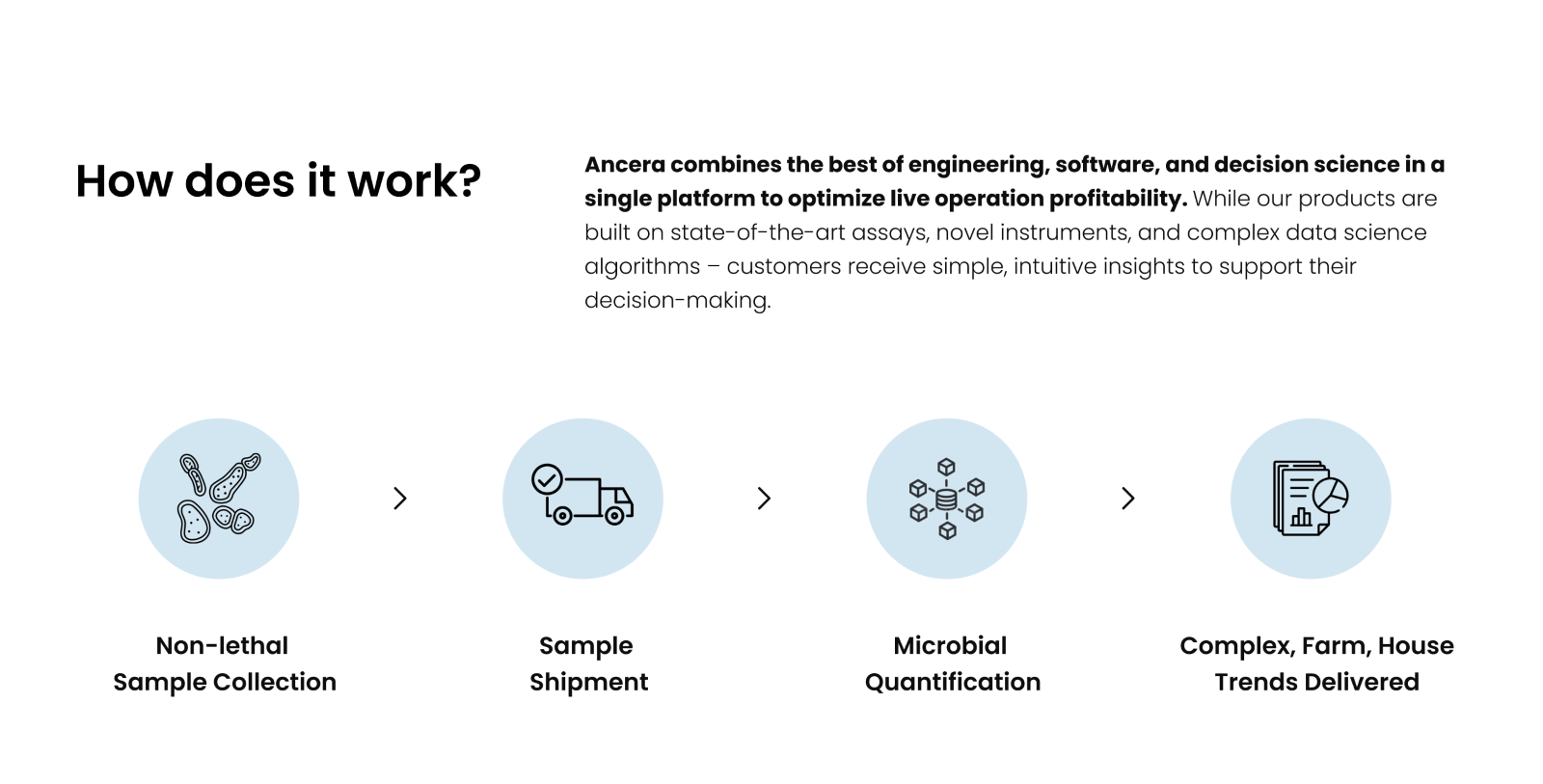
Adjacent to the engineering lab was a “PIPER Museum” where you could see the physical evolution of Ancera’s hardware platform. While each iteration added complex new features (modular cartridges, IoT connectivity, digital interfaces, etc.) they exterior design’s evolution was focused on simplicity and elegance.
The prospect of visiting the lab in the near future with today’s PIPER model sitting in the museum made me appreciate the breakneck pace of innovation.
Novel diagnostics are hardware-enabled, but software-defined.
Next time, we’ll talk to Ancera’s Head of Data Science and learn how the data collected from the PIPER is analyzed and transformed into models that are used to manage millions of live birds each week.